The Impact of Material Choices on Needle Roller Bearing Performance
- qianzhoumachinery
- Jul 24, 2024
- 3 min read

The heart of a needle roller bearing's performance lies in the materials meticulously chosen for its construction. From the slender rollers to the encasing rings, each component is gravely important for determining the bearing's lifespan, load-carrying capacity, and operational efficiency.
The Roller's Crucial Role
The needle rollers, those tiny cylindrical warriors, bear the brunt of the load. The material composition of these rollers significantly influences the bearing's overall performance:
Through-Hardened Steel:
This industry standard offers a robust balance of hardness with toughness, making it suitable for a wide range of applications.
Carbon and alloy steels are cost-effective options and provide adequate performance in less demanding environments.
Stainless Steel:
For applications exposed to corrosive elements, stainless steel rollers offer superior resistance to rust and oxidation.
Ceramic:
This high-tech material boasts exceptional hardness and wear resistance, making it ideal for demanding conditions where longevity is paramount.
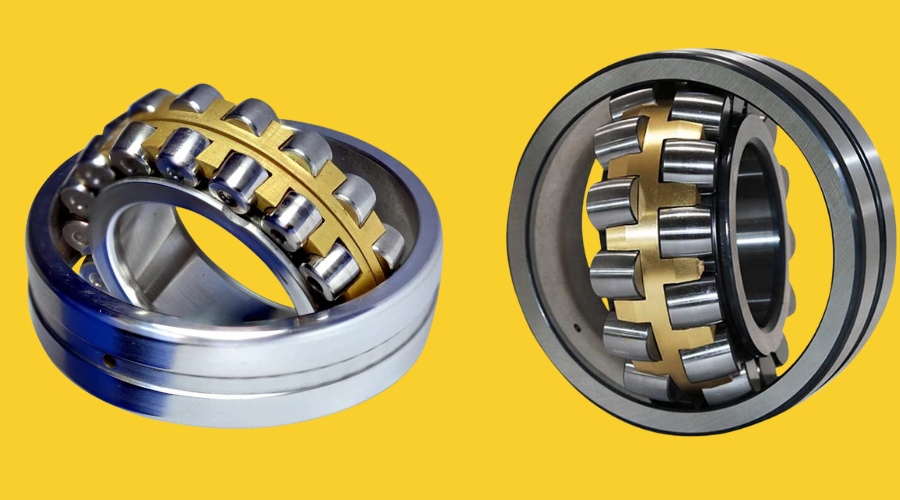
The Raceways: The Bearing's Foundation
The raceways, the tracks on which the rollers glide, are equally critical. The material of these rings influences the bearing's durability and load-handling capacity:
Through-Hardened Steel:
Often paired with through-hardened rollers, this material provides a solid foundation for the bearing.
Case-Hardened Steel:
Case-hardened steel enhances wear resistance while maintaining structural integrity by offering a hard exterior and rigid core.
Ceramic:
Combined with ceramic rollers, ceramic raceways create an ultra-low friction environment, ideal for high-performance applications.
The Cage: The Bearing's Protector
The cage, the often-overlooked component, plays a crucial role in maintaining roller spacing and preventing contact. The material choice impacts the cage's durability and operational efficiency:
Steel:
The most common option is steel cages, which offer good strength but can be noisy in high-speed applications.
Brass:
Provides better wear resistance and quieter operation compared to steel cages.
Polyamide:
Plastic material is known for its quiet operation and good wear resistance, especially in high-speed environments.
Material Synergies: The Perfect Blend
The performance of a needle roller bearing is not solely determined by the individual materials but also by their interaction. A harmonious blend of materials is essential for optimal results. For instance, combining ceramic rollers with steel raceways can create a bearing that excels in wear resistance and load-carrying capacity.
Material Selection: Key Considerations
When choosing materials for a needle roller bearing, several factors come into play:
Load Capacity: The bearing must handle the expected load without compromising performance.
Operating Speed: High-speed applications demand materials with superior heat resistance and fatigue strength.
Operating Environment: Some factors, such as temperature, humidity, and exposure to corrosive substances, influence material selection.
Cost: Material costs vary, and the overall bearing cost must be balanced against performance requirements.
By carefully considering these factors and working closely with a Needle Roller Bearing distributor, engineers can select the optimal materials for their specific application, ensuring maximum bearing life and equipment reliability.
Frequently Asked Questions
What is the most common material for needle roller bearings?
Through-hardened steel is widely used for both rollers and raceways.
Can I mix and match materials for different components?
Yes, material combinations can be tailored to specific application requirements.
How do I choose the suitable material for my bearing?
Consider load, speed, operating environment, and cost when selecting materials.
The judicious selection of materials is the cornerstone of high-performance needle roller bearings. Engineers can optimize bearing performance and extend equipment life by understanding the characteristics and interplay of different materials.
Comments