Are Needle Bearings Better Than Ball Bearings?
- qianzhoumachinery
- Feb 23, 2024
- 3 min read
Updated: May 13, 2024

The debate between needle and ball bearings has raged in the machinery and mechanical systems world. Both types of bearings serve essential roles in various applications, each with advantages and disadvantages. Let's dive into the intricacies of needle and ball bearings to determine which reigns supreme in engineering excellence.
Unraveling the Mechanics: Understanding Needle Bearings
Imagine a slender needle piercing through fabric with precision and finesse, much like its namesake; a needle bearing features long, cylindrical rollers that offer increased surface contact and load-bearing capacity. These rollers, housed within a compact assembly, provide excellent radial and axial support, making needle bearings ideal for applications with high radial loads and limited space.
Embracing Sphericity: The World of Ball Bearings
Visualize a sphere rolling effortlessly along a smooth surface with fluid and frictionless movements. Ball bearings harness the power of spherical rolling elements to facilitate smooth rotation and reduce friction within machinery. With their spherical shape, ball bearings distribute loads evenly and accommodate radial and axial forces, making them versatile and adaptable to various applications.
Load Capacity Showdown: Comparing Needle Bearings and Ball Bearings
Needle Bearings: Strength in Size
Auditorily, needle bearings excel in applications where space is at a premium. Their slender rollers boast a larger contact area than ball bearings, allowing them to withstand higher radial loads without sacrificing compactness. This makes needle bearings the preferred choice for applications such as automotive transmissions, where space constraints and heavy loads are expected.
Ball Bearings: Versatility and Efficiency
In contrast, ball bearings offer versatility and efficiency across various applications. Their spherical rolling elements distribute loads evenly, reducing friction and wear while promoting smooth rotation. Ball bearings are commonly found in machinery ranging from industrial equipment to household appliances, where reliability and performance are paramount.
Friction Factor: Examining Efficiency and Durability
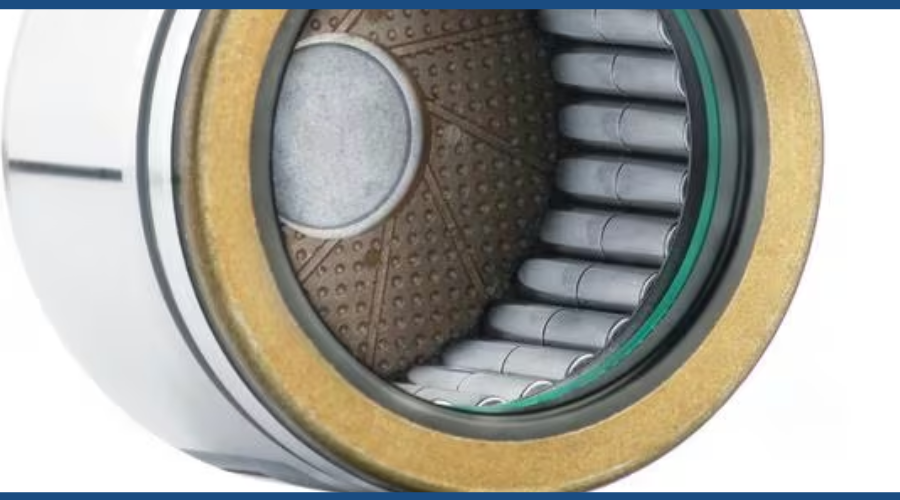
Needle Bearings: Minimizing Friction, Maximizing Efficiency
Visually, the elongated shape of needle rollers reduces contact surface area, resulting in lower friction and energy consumption. This makes needle bearings highly efficient in applications requiring high-speed operation or frequent oscillation, where minimizing frictional losses is crucial for optimal performance and longevity.
Ball Bearings: Balancing Load Distribution and Wear Resistance
In contrast, ball bearings balance load distribution and wear resistance. Their spherical shape allows smooth rolling motion, reducing friction and wear on bearing surfaces. While ball bearings may exhibit slightly higher friction compared to needle bearings, they excel in applications with moderate to high speeds and varying load conditions.
The Verdict: Choosing the Right Bearing for Your Application
There is no one-size-fits-all answer when selecting between needle and ball bearings. Each bearing type offers unique advantages and is best suited for specific applications. Needle bearings excel in scenarios with high radial loads and limited space, while ball bearings thrive in applications requiring versatility, efficiency, and smooth operation.
FAQs
Q: How do needle and ball bearings differ in design and application?
A: Needle bearings feature elongated rollers for increased load-bearing capacity in tight spaces, which is ideal for high radial loads. With their spherical design, ball bearings offer versatility and even load distribution across various applications.
Which type of bearing is better for high-speed applications?
A: Needle bearings are preferred for high-speed applications due to their reduced friction and energy consumption. Their elongated rollers minimize contact surface area, enabling smoother operation at elevated speeds.
How do I determine the correct type of bearing for my specific application?
A: Consider load requirements, space constraints, operational conditions, and desired performance characteristics. Being aware of each type of bearing's unique features and capabilities will make it easier to make an informed decision that fits your application's requirements.
Conclusion: Harnessing the Power of Precision Bearing
Choosing between needle and ball bearings in engineering relies on load, space, and operational factors. Understanding each bearing's features allows engineers to optimize performance and reliability. Partnering with a trusted wholesale Needle Roller Bearing supplier ensures access to tailored, quality components for smoother operations.
Comments